The warehouse market is booming. The ubiquity of online retailers has kept warehouse space in high demand throughout the commercial real estate push-and-pull of recent years. So, if you’re looking to jump on board and look for new warehouse space (or optimize existing properties), look no further.
As Tenant Reps, we are commercial real estate experts. Our industry experience has equipped us with the appropriate market knowledge to know how to find the perfect warehouse space and get the best deal in the process. So read on to prepare yourself with the ultimate checklist for warehouse space. You’ll learn the ins and outs, everything you should consider when searching, touring, or developing the perfect corporate warehouse environment.
Size and Shape of the Layout
Size matters when it comes to warehouse space. You need to ensure that you can store the maximum products in the most efficient manner. Before you begin your property search, you should be absolutely clear on the amount of cubic storage your company requires.
Not only must you accommodate for inventory, but also the size of the workforce. On top of this, you must think about working environments. For example, does the warehouse have an office space… what about common areas and bathrooms? Don't overlook these features in the warehouse checklist.
The layout of the space will work around the warehouse’s column placing. Columns are generally spaced 40' to 50' apart. Keep in mind that this is an integral feature in determining the optimal workflow, storage capacity, and racking. This is an unavoidable feature to examine when identifying your racking requirements.
Proper racking is the backbone of an efficient warehouse. Not only does it need enough height to maximize storage, but it must work within the existing floor plan to optimize the existing space. This means considering factors including the depth of the rack, flue spacing, and aisle width. Know that 50% of the market utilizes 64" pallets.
In examining aisle width, a 54' column spacing allows for a 10' aisle with 48" racking. When this spacing increases to 60' between each column, the aisles widen from 10' to 12', creating wasted space.
Challenges then emerge from poor space utilization and decreased storage locations for racking. Aisles must also be easily maneuverable for heavy equipment and workflows. Also, consider where any possible obstructions lie- not only for productivity but safety as well. The facility should have adequate entrances and exits.
Flooring
Flooring is simple, right? Well, when it comes to industrial warehouse flooring, things get a little more complex. The central concern with your warehouse flooring is ensuring that it can handle the weight of your inventory, racking, and heavy machinery. Typically, concrete flooring is poured in 4" or 6" slabs.
For context, a 2" concrete slab can hold 740 psi of weight. This number increases to 1,105 psi for a 6" pour and 1,194 psi for a 7" pour. Deciding on the proper fill for your inventory will avoid nightmares brought on by exceeding the concrete’s weight capacity. Overloading your slabs will cause significant floor cracking.
Remember that floor imperfections are severely magnified when your inventory is stored 30 feet high. |
To avoid flooring catastrophes, developers traditionally use 6" floor slabs for 28' foot to 32' clear buildings.
You must also consider the finish of the flooring. Typically, warehouses have polished or epoxy finishes. While epoxy is generally more durable and longer lasting, it is more expensive. On the other hand, polished floors are more affordable but cannot withstand as much weight. So, if you are servicing heavier inventory or a highly trafficked floor, epoxy may be worth the investment.
Ceilings
Like flooring, your warehouse ceilings cannot be overlooked. The right ceiling height is integral to your storage. How much room do you have to stack your goods safely? Determine the property’s clear stack height, or the usable height for storing shelving and inventory.
In the industry, 32’ ceiling heights have been standard, however, as tenants like Amazon move towards optimizing cubic storage over square footage, this number has risen to 36’ clear height buildings. By doing so, a tenant can increase the capacity of a warehouse by 10% to 25%. These higher clear height warehouses are typically Class A warehouses and come at a premium. That said, the efficiency they provide may be well worth it.
Racking
Low ceiling heights limit the goods and equipment a warehouse can service. To arrive at your optimal ceiling height, examine your need for racking. Generally, a 32’ ceiling can stack between 4 to 6 pallets high.
If your ceiling height does not provide adequate racking space, you may have the option to raise the ceiling. Know that this typically would cost around $5 psf to $25 psf, but costs can widely vary according to your property’s state, the area you’re in, and many other factors. Be prepared for your contractor to advise you to demolish and start from scratch.
State of the Roof
On a similar note, you must consider the state of the building’s roof. This is especially true for older warehouses. The typical lifespan of warehouse roofing is ~20 years. If your property is coming up on this benchmark, note this as a point of negotiation for your tenant improvement allowance.
A high-integrity roof is a non-negotiable for warehouse space that easily holds millions of dollars in inventory. |
Utilities
The utilities in your warehouse will depend heavily on your production and inventory’s unique requirements. They also go a long way to creating the most efficient and comfortable environment.
Water and Sprinkler Systems
Are the property’s water supply and drain lines in working order? Water requirements are especially pertinent for warehouses because of safety and fire codes. The type of inventory you are storing will decide the sprinkler system you need. Options include:
- Wet systems
- Dry systems
- Pre-action systems
- Foam systems
- Quell systems
The most common types are wet and dry. Wet are traditional sprinkler systems in piping. Within this category, you also have the option for Early Suppression Fast Response (ESFR) which focuses more volume on the fire's origin. ESFR sprinkler systems provide twice the amount of water than traditional wet sprinklers (60 gallons per minute), whereas conventional sprinkler heads unleash 25 to 30 gallons per minute. ESFR systems are typically used to protect high-piled or palletized inventory.
Image source: baroneq.com
Similarly, are quell sprinkler systems that adopt a "surround and drown" approach to fire hazards. A massive volume of water is unleashed to put out fires quickly and minimize heat damage.
Dry sprinklers are optimal for water-sensitive equipment. They are often seen also in unheated warehouses where water in piping is susceptible to freezing. One big point to check is your insurance! What type of sprinkler system does it call for? If you are uncertain, then call your broker or carrier before starting your search.
HVAC
Depending on what you’re storing, proper HVAC can be a key concern for a warehouse. This is especially true if your materials must be kept at a certain temperature. Are there heating or air conditioner requirements… Do specific items need to be stored in a freezer?
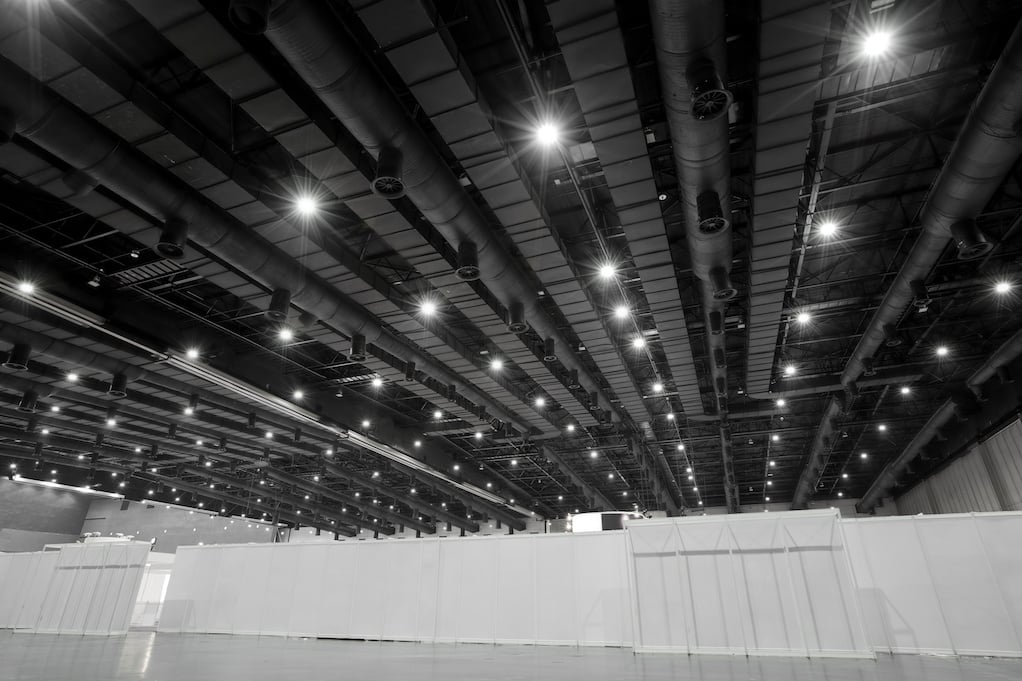
There must also be sufficient ventilation-not only for your products but your team members. The comfort and safety of your employees should always be your top concern.
Electric
Is there appropriate electric capacity to support production? One must consider the power needs not only for lighting but also conveyors, automation, other equipment, and all of their charging requirements.
It's also a good idea to back up your electrical requirements with generators. This is especially true for environments that service temperature-sensitive goods.
Accessibility
A main concern of warehouse space is always how accessible it is. How conveniently can inventory, equipment, and vendors reach your site? When shipping turnaround times are plummeting as consumers expect quick service and delivery, the accessibility of warehouses is becoming more demanding.
Is it close to major highways? Do those highways have overpass height limitations that may obstruct shipping? Do you require access to rails or barges? What about the access roads- can they handle the weight of your truck loads?
Ensuring that your warehouse is close to shipping channels should be a key site driver in your property search.
Parking
Another access consideration is the parking ratio of your warehouse. Will trucks carrying equipment have enough room to park safely when they reach your facility? Not only this, but will your truck beds have enough room to navigate and turn around in your lot?
The average trailer size is 48 feet to 53 feet long. A semi-trailer requires a ~55 by 14-foot space for storage. For trucks and trailers, this number is bumped up to 75 by 14 feet.
What about vendors or employees? Your warehouse parking ratio must balance the demand for truck spots with car parking. Generally, warehouse parking ratios should provide three or four car spots per thousand square feet.
Loading Docks
Last but certainly not least is loading. Warehouses can’t only accommodate truck parking but servicing as well. As such, the loading docks are a vital feature of every warehouse. The size and location of the loading docks must be accessible for your carriers. If you’re handling palletized freight, you will likely also require a dock leveler for efficient loading and unloading. Not only do levelers streamline production time, but they reduce hazards. They bridge the trailer and warehouse for a safe transfer of goods.
To determine the right loading dock, you must consider what your needs are. What are the heights and widths of the truck beds? How will the docks' design affect the truck's approach and positioning? There are four major types of loading docks, each with their own pros and cons:
- Flush Loading Dock
- Enclosed Loading Dock
- Open Loading Dock
- Sawtooth Loading Dock
Flush docks are the most common type. They act as an opening within the warehouse wall that is usually equipped with bumpers.
Image source: Freightera
Open docks are also for outdoor use, but they are often seen with a canopy or roof. However, they are not seen as often as flushed docks.
Image source: Freightera
Enclosed docks are within the warehouse and good for temperature-sensitive equipment, but they require ventilation to get rid of the enclosed truck exhaust. As such, they are not as common.
Image source: Freightera
Also rarely seen are sawtooth docks, which are usually present when outdoor maneuvering space for trucks is limited. It allows them to park at an angle but comes with the disadvantage of poor space utilization.
Image source: Freightera
Find the Optimal Warehouse with a Tenant Rep
As you can see, there are many things to consider when finding warehouse space. Luckily, you don’t need to balance these factors alone. As Tenant Reps at iOptimize Realty®, we have 30+ years of experience finding the best properties, terms, and prices for our corporate tenants. Our market knowledge equips us to leverage your requirements against each property’s features to land the space that is the optimal fit for your business.
So, if you don’t want to worry about pallet racking or concrete slabs, you don’t have to! Let us take the weight of warehouse decisions off your shoulders.
Ready to hear how a Tenant Rep can help you today? Schedule a meeting now.